一、技術(shù)性能升級:精度與效率飛躍
1、 Technical performance upgrade: leap in accuracy and efficiency
復合精度突破
Breakthrough in Composite Accuracy
傳統(tǒng)設(shè)備:依賴人工調(diào)校,復合層間間隙誤差±0.3mm以上,易導致門窗型材隔熱條/密封條脫層
Traditional equipment: relying on manual calibration, the gap error between composite layers is more than ± 0.3mm, which can easily lead to delamination of insulation/sealing strips of door and window profiles
新一代滾壓復合機:
New generation rolling composite machine:
采用 高剛性伺服壓輥系統(tǒng),壓力波動≤±1.5%,層間貼合精度達±0.05mm
Adopting a high rigidity servo roller system, the pressure fluctuation is ≤± 1.5%, and the interlayer bonding accuracy reaches ± 0.05mm
內(nèi)置 激光實時糾偏裝置,自動修正材料跑偏(如鋁塑復合帶偏移超0.1mm即觸發(fā)調(diào)整)
Built in laser real-time correction device, automatically correcting material deviation (such as triggering adjustment when the deviation of aluminum-plastic composite tape exceeds 0.1mm)
生產(chǎn)速度倍增
Double the production speed
傳統(tǒng)設(shè)備:單機線速8-10米/分鐘,換型需停機2小時調(diào)整模具
Traditional equipment: Single machine line speed of 8-10 meters per minute, requiring a 2-hour downtime to adjust the mold for mold changing
升級機型:
Upgrade model:
線速提升至 15-20米/分鐘(同比提速60%以上)
The line speed has been increased to 15-20 meters per minute (with a year-on-year increase of over 60%)
快速換型模塊:通過預裝模具庫+液壓快換系統(tǒng),切換材料規(guī)格僅需15分鐘
Quick change module: By pre installing the mold library and hydraulic quick change system, switching material specifications only takes 15 minutes
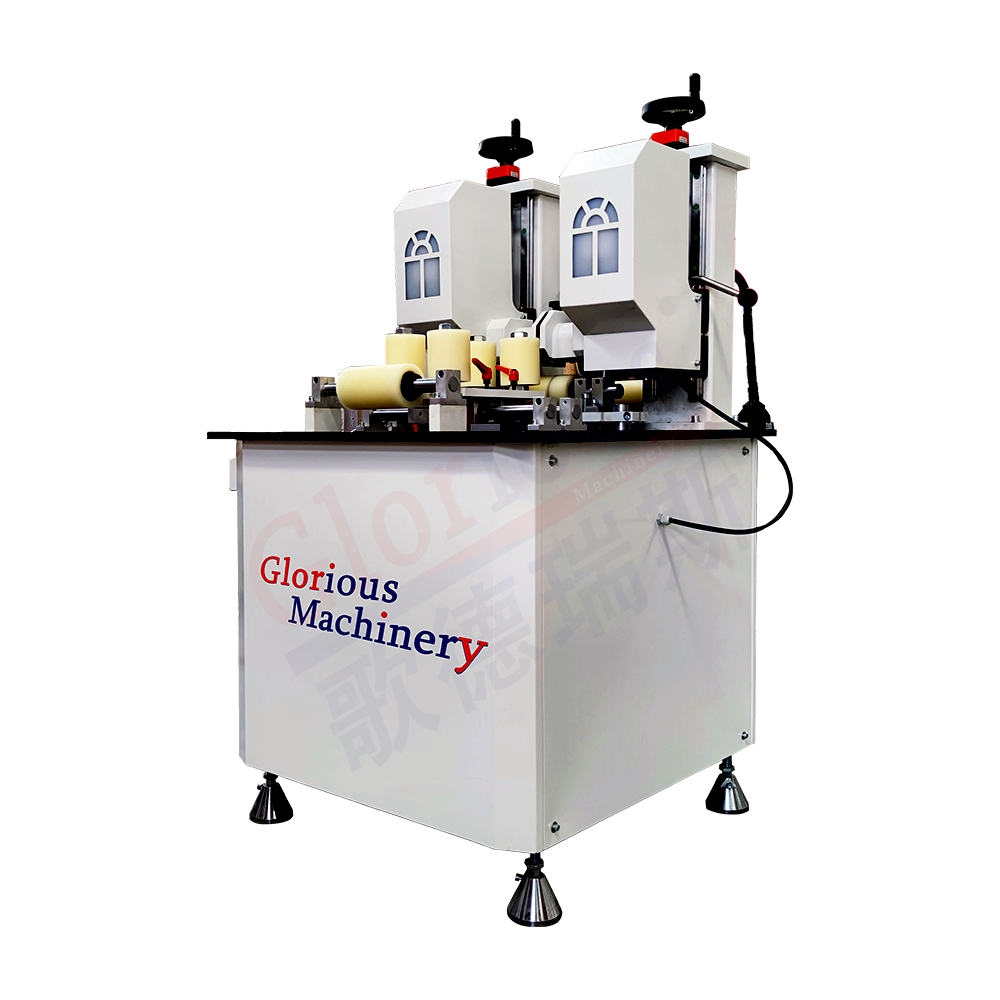
二、智能化與節(jié)能優(yōu)勢
2、 Intelligent and energy-saving advantages
智能控制系統(tǒng)降本增效
Intelligent control system reduces costs and increases efficiency
工藝參數(shù)自學習:根據(jù)材料厚度、張力自動優(yōu)化滾壓壓力與溫度(如PVC/鋁材復合溫度精準控溫±2℃)
Self learning of process parameters: automatically optimize rolling pressure and temperature based on material thickness and tension (such as precise temperature control ± 2 ℃ for PVC/aluminum composite)
能耗監(jiān)控系統(tǒng):實時顯示每米加工電耗,同比傳統(tǒng)設(shè)備節(jié)能25%-30%(以日均生產(chǎn)5000米計算,年省電費超12萬元)
Energy consumption monitoring system: Real time display of power consumption per meter of processing, saving 25% -30% energy compared to traditional equipment (calculated based on daily production of 5000 meters, saving over 120000 yuan in annual electricity bills)
數(shù)字化生產(chǎn)管理
Digital Production Management
接入 MES系統(tǒng),實時生成復合層厚度、瑕疵點分布報告,支持質(zhì)量追溯
Integrate with MES system to generate real-time reports on composite layer thickness and defect distribution, supporting quality traceability
異常停機自動推送報警至手機(如軸承溫度超65℃、潤滑油壓力不足)
Abnormal shutdown automatic push alarm to mobile phone (such as bearing temperature exceeding 65 ℃, insufficient lubricating oil pressure)
三、材料兼容性與成品質(zhì)量提升
3、 Material compatibility and improvement of finished product quality
多材料復合能力擴展
Multi material composite capability expansion
傳統(tǒng)局限:僅能處理鋁塑、鋼塑等常規(guī)組合,且材料厚度范圍窄(如鋁帶厚度0.3-0.8mm)
Traditional limitations: It can only handle conventional combinations such as aluminum-plastic and steel plastic, and the material thickness range is narrow (such as aluminum strip thickness of 0.3-0.8mm)
新一代設(shè)備突破:
New generation device breakthrough:
支持 金屬/非金屬超薄復合(如0.15mm鋁箔+0.1mmPET膜)
Support metal/non-metal ultra-thin composite (such as 0.15mm aluminum foil+0.1mm PET film)
可加工 異型復合材料:曲面、波浪紋等特殊結(jié)構(gòu)一次成型
Machinable irregular composite materials: one-time molding of special structures such as curved surfaces and wavy patterns
成品強度與耐久性優(yōu)化
Optimization of finished product strength and durability
通過 梯度滾壓技術(shù),實現(xiàn)材料界面分子級結(jié)合,剝離強度提升50%以上(實測達35N/cm?)
By using gradient rolling technology, molecular level bonding at the material interface is achieved, and the peel strength is increased by more than 50% (measured to reach 35N/cm?)
復合界面無氣泡、無褶皺,門窗型材耐候壽命從10年延長至15年
The composite interface has no bubbles or wrinkles, and the weather resistance life of door and window profiles has been extended from 10 years to 15 years
四、運維成本大幅降低
4、 Significant reduction in operation and maintenance costs
維護便捷性升級
Upgrade maintenance convenience
傳統(tǒng)痛點:齒輪箱需每周加注黃油,滾軸磨損每3個月更換,停機損失大
Traditional pain points: The gearbox needs to be filled with butter every week, the rollers wear out and need to be replaced every 3 months, resulting in significant downtime losses
改進方案:
Improvement plan:
自潤滑軸承+陶瓷涂層輥筒:維護周期延長至6個月
Self lubricating bearings+ceramic coated rollers: maintenance cycle extended to 6 months
模塊化設(shè)計,更換關(guān)鍵部件僅需30分鐘(傳統(tǒng)需拆機4小時)
Modular design, replacing key components only takes 30 minutes (traditional requires 4 hours of disassembly)
本文由滾壓復合機友情奉獻.更多有關(guān)的知識請點擊:http://www.hotse.cn我們將會對您提出的疑問進行詳細的解答,歡迎您登錄網(wǎng)站留言.
This article is dedicated to friendship For more information, please click: We will provide detailed answers to your questions. You are welcome to log in to our website and leave a message