1. 自動化上下料,減少人工干預(yù)
1. Automated loading and unloading to reduce manual intervention
自動穿條功能通過機械裝置實現(xiàn)型材和隔熱條的自動上料與下料,取代了傳統(tǒng)的人工操作。例如,山東途順數(shù)控設(shè)備有限公司的隔熱型材數(shù)控高速自動穿條機,通過傳送輥和抓夾裝置實現(xiàn)型材的自動輸送和固定,減少了人工搬運的時間和勞動強度。這種自動化設(shè)計不僅提高了生產(chǎn)效率,還降低了工傷風險。
The automatic threading function achieves automatic feeding and unloading of profiles and insulation strips through mechanical devices, replacing traditional manual operations. For example, Shandong Tushun CNC Equipment Co., Ltd.'s insulation profile CNC high-speed automatic threading machine achieves automatic transportation and fixation of profiles through conveyor rollers and gripping devices, reducing the time and labor intensity of manual handling. This automated design not only improves production efficiency, but also reduces the risk of work-related injuries.
2. 高精度與高速度加工
2. High precision and high-speed machining
自動穿條功能通常配備高精度的機械部件和控制系統(tǒng),能夠快速、準確地完成穿條任務(wù)。例如,荷蘭機械公司的穿條機通過優(yōu)化設(shè)計,可在30秒內(nèi)完成一個輪轂的加注工作。此外,自動穿條機的加工精度更高,減少了因人為操作失誤導(dǎo)致的廢品率,進一步提高了生產(chǎn)效率。
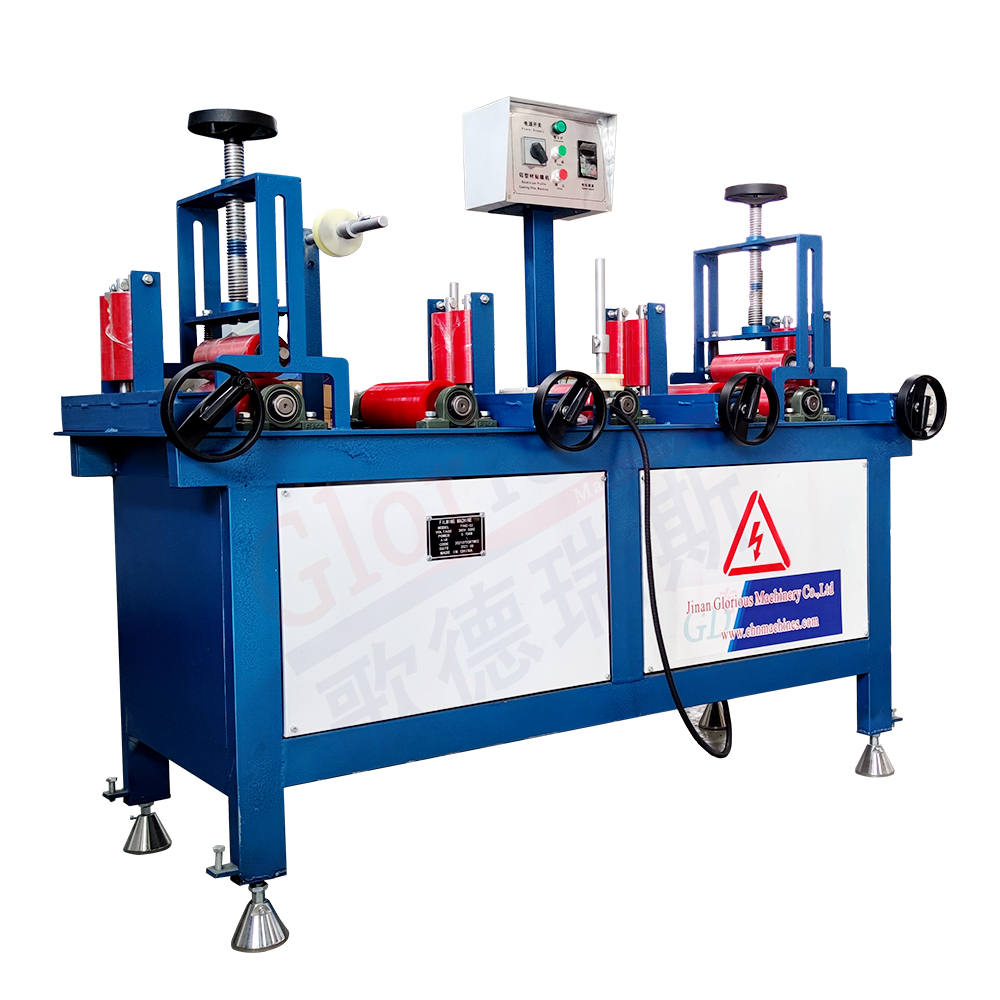
The automatic threading function is usually equipped with high-precision mechanical components and control systems, which can quickly and accurately complete the threading task. For example, the threading machine of a Dutch machinery company can complete the filling of a wheel hub within 30 seconds through optimized design. In addition, the processing accuracy of the automatic threading machine is higher, reducing the scrap rate caused by human operation errors and further improving production efficiency.
3. 多工序集成,優(yōu)化生產(chǎn)流程
3. Multi process integration to optimize production processes
開齒穿條一體機將開齒和穿條工序集成在同一設(shè)備中,減少了設(shè)備之間的轉(zhuǎn)運時間和操作步驟。例如,一些新型設(shè)備在開齒的同時直接完成隔熱條的穿入,大大縮短了加工周期。這種集成化設(shè)計不僅提高了生產(chǎn)效率,還降低了設(shè)備占地面積。
The integrated machine for cutting teeth and threading strips integrates the cutting and threading processes into the same equipment, reducing the transfer time and operation steps between devices. For example, some new devices directly insert the insulation strip while opening the teeth, greatly reducing the processing cycle. This integrated design not only improves production efficiency, but also reduces equipment footprint.
4. 靈活性與適應(yīng)性提升
4. Flexibility and adaptability improvement
自動穿條功能通過數(shù)控系統(tǒng)和可調(diào)節(jié)的機械結(jié)構(gòu),能夠快速適應(yīng)不同規(guī)格和尺寸的型材。例如,某些設(shè)備通過電機驅(qū)動和調(diào)節(jié)機構(gòu),可快速切換不同高度的型材,無需頻繁更換刀具或調(diào)整設(shè)備。這種靈活性顯著提高了設(shè)備的利用率和生產(chǎn)效率。
The automatic threading function can quickly adapt to profiles of different specifications and sizes through a CNC system and adjustable mechanical structure. For example, some devices can quickly switch between profiles of different heights through motor-driven and adjustable mechanisms, without the need for frequent tool changes or equipment adjustments. This flexibility significantly improves the utilization and production efficiency of the equipment.
5. 降低勞動成本
5. Reduce labor costs
自動化穿條功能減少了對熟練工人的依賴,降低了人力成本。例如,格力電器的自動穿毛條及壓彎裝置通過自動化操作,減少了人工干預(yù),同時提高了生產(chǎn)精度。這種技術(shù)的應(yīng)用不僅提高了生產(chǎn)效率,還為企業(yè)帶來了顯著的成本效益。
The automated threading function reduces reliance on skilled workers and lowers labor costs. For example, Gree Electric's automatic threading and bending device reduces manual intervention and improves production accuracy through automated operation. The application of this technology not only improves production efficiency, but also brings significant cost-effectiveness to enterprises.
6. 實時監(jiān)控與數(shù)據(jù)反饋
6. Real time monitoring and data feedback
一些自動穿條設(shè)備配備了先進的控制系統(tǒng),能夠?qū)崟r監(jiān)控生產(chǎn)過程中的各項數(shù)據(jù),確保每一步操作的精準性。這種動態(tài)反饋機制不僅優(yōu)化了生產(chǎn)流程,還為設(shè)備的維護和故障排查提供了支持。
Some automatic threading devices are equipped with advanced control systems that can monitor various data in real-time during the production process, ensuring the accuracy of each step of the operation. This dynamic feedback mechanism not only optimizes the production process, but also provides support for equipment maintenance and troubleshooting.
綜上所述,自動穿條功能通過自動化、高精度、集成化和靈活性等多方面的技術(shù)優(yōu)勢,顯著提高了生產(chǎn)效率,降低了成本,同時提升了產(chǎn)品質(zhì)量和生產(chǎn)安全性。
In summary, the automatic threading function has significantly improved production efficiency, reduced costs, and enhanced product quality and production safety through various technological advantages such as automation, high precision, integration, and flexibility.